After a lot of painstaking formwork construction and the addition of a post tensioning reinforcement grid, the section 1 portion of the first structured floor was ready for concrete. This view, taken about the middle of November shows the formwork section to be poured, with the grade-level section 2 slab already in place to the left.
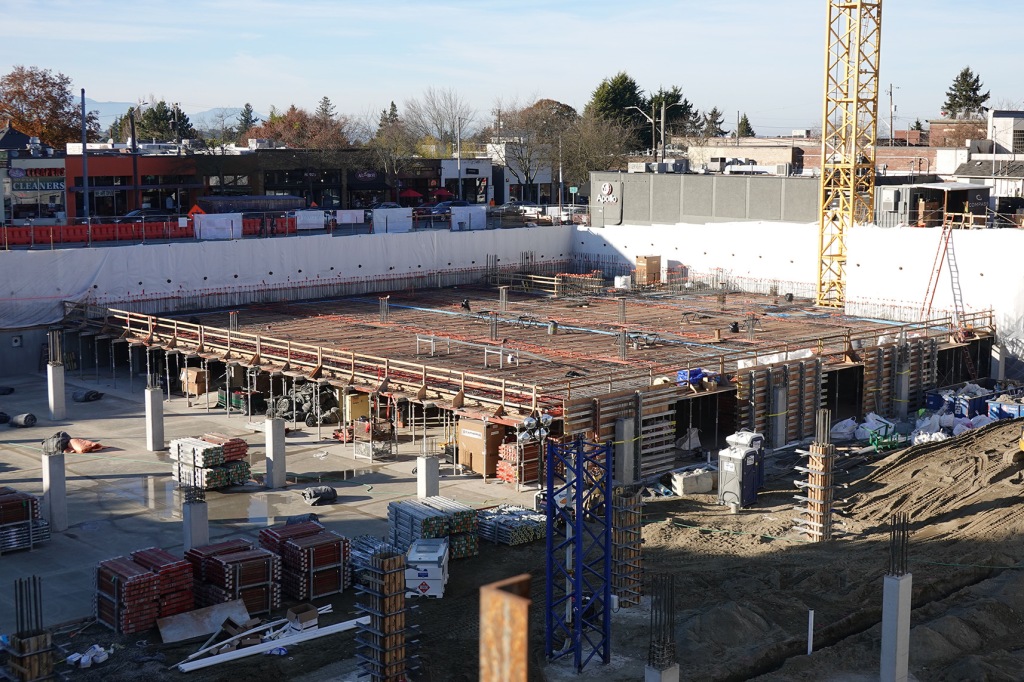
A quiet Thanksgiving day gave the crew a couple days off. Note that, in contrast to the photo above, the PT formwork for section 2 is now in place in the foreground, though it doesn’t have any reinforcing as yet.

To give you a road map, I’ve outlined the first four sections: section 1 being poured, section 2 about to receive reinforcing grid, section 3 getting crushed stone, capillary break for its ground level slab, and section 4 providing support area for materials and equipment.
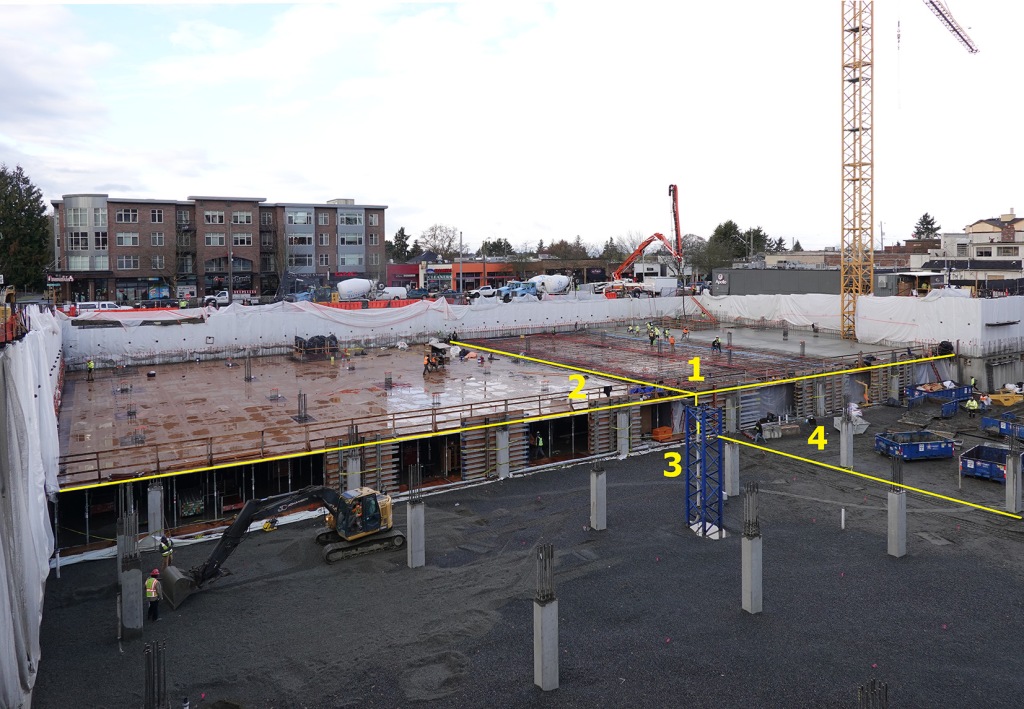
The pour starts up on Queen Anne Avenue, where pairs of concrete trucks deliver the mix to the pumping truck. A line of concrete trucks is staged around the block; and as soon as one has delivered its load, another replaces it.

It’s an intense area to be in, what with the large size of the equipment and the amount of vibration in a compact space.

The pumping arm reaches a long distance and from this position the delivery seems delicate. The area in the foreground has already been poured and is getting final touches.

But when you get closer, you realize that the delivery end of the hose is where the action is. As you can see, the concrete is really fluid. Often additives are used to insure that it stays fluid all the way from the truck and does not clog the line.
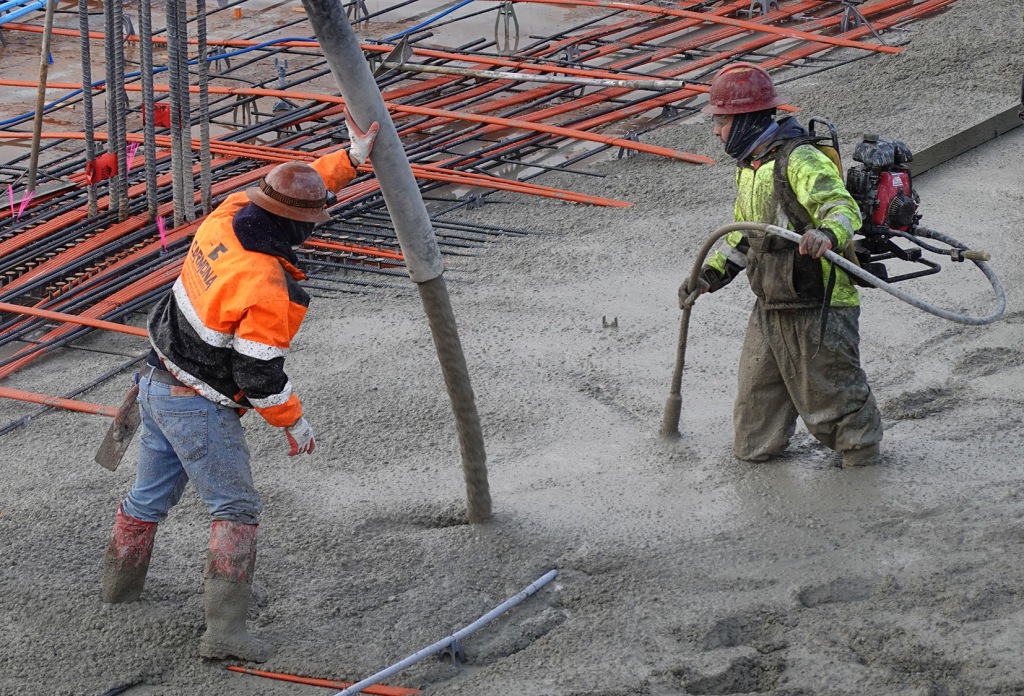
Before the smoothing crews get going a couple of key steps are required. The concrete has to be vibrated in ensure that it flows completely through the network of reinforcing and post-tensioning cables. Reinforced concrete works well only if it completely bonds with the reinforcing; and the vibration (man upper photo – right and lower photo – left) assures that it happens. One other key control element is assurance that the concrete is the correct thickness. The man in the green shirt on the right, below, is using a control stick with a gauge with which he frequently checks the depth.

Leveling, it turns out, is mostly a hand operation in the early stages because the concrete is too fluid to support any equipment. Here it involves two-man screed-board teams, supported by others who can add concrete to low spots as the leveling takes place.

In the case below, two men using individual screeding tools adjust the amount of concrete available to be leveled, adding and subtracting as the screed board is moved. Note that the guides are the screed board at 90 degrees on the right and the surface of the previously leveled slab on the left.
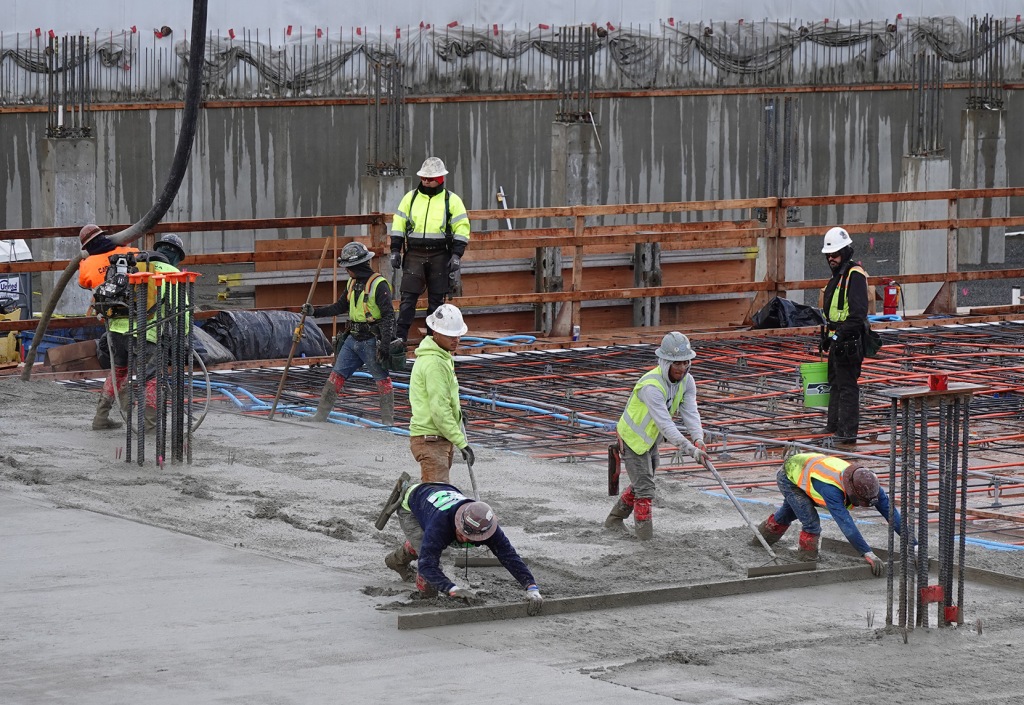
What is amazing, as shown in the picture below, is that the concrete is fluid enough that they’re in it up to their shins, and at the same time it’s firming up enough fast enough to be leveled and hold its position. Timing is everything; and the concrete is in charge.

Following at a discrete time and distance behind the pouring and screeding is the surface smoothing, using double-bladed riding machine that moves quickly in a variety of directions, followed by a smaller, hand-guided machine where the concrete has gotten firm enough for the worker to walk on the slab. Another worker over near the wall applies a final careful touch with a smoothing blade on the end of a 20′ long pole.

And finally, since the installation has been done in broad bands across the whole area, there’s some careful touch-up work applied at the joints.

Given how much hand work is involved, it’s impressive how well the finished slab turns out.

Finally, just a reminder that while today’s “excitement” was happening in section 1, sections 3, 4 and 5 have been busy as well. We’ll catch up with them soon.