
For a number of months we’ve watched the 21 Boston / Gables Queen Anne project exterior come into shape, partially hidden by scaffolding and mesh. Now things are changing and we’re getting a look at what’s coming. In this view we get a look at the north end of Building C, the one that runs along Queen Anne Avenue, where Hardi-board siding (light yellow) has been installed from a movable scaffolding (It will be painted).
But just this week the project started to reveal some of the finishes on the Queen Anne Avenue side. In this case the upper level façade is now black and the cream-colored brick stands out below it. The scaffolding has provided floor-level working platforms for the masons as well as delivery of materials.

With these finishes established, the scaffolding can come down, accomplished here by dismantling the pieces one at a time and stacking them on the platforms.

The sequencing of this activity is a delicate dance, in that the scaffolding is all diagonally braced. The other pieces the diagonals stabilize have to be removed first, and importantly, people doing the work have to be careful not to exert unexpected movements on the structure. Some of the pieces are stacked where the tower crane bucket can take them away.
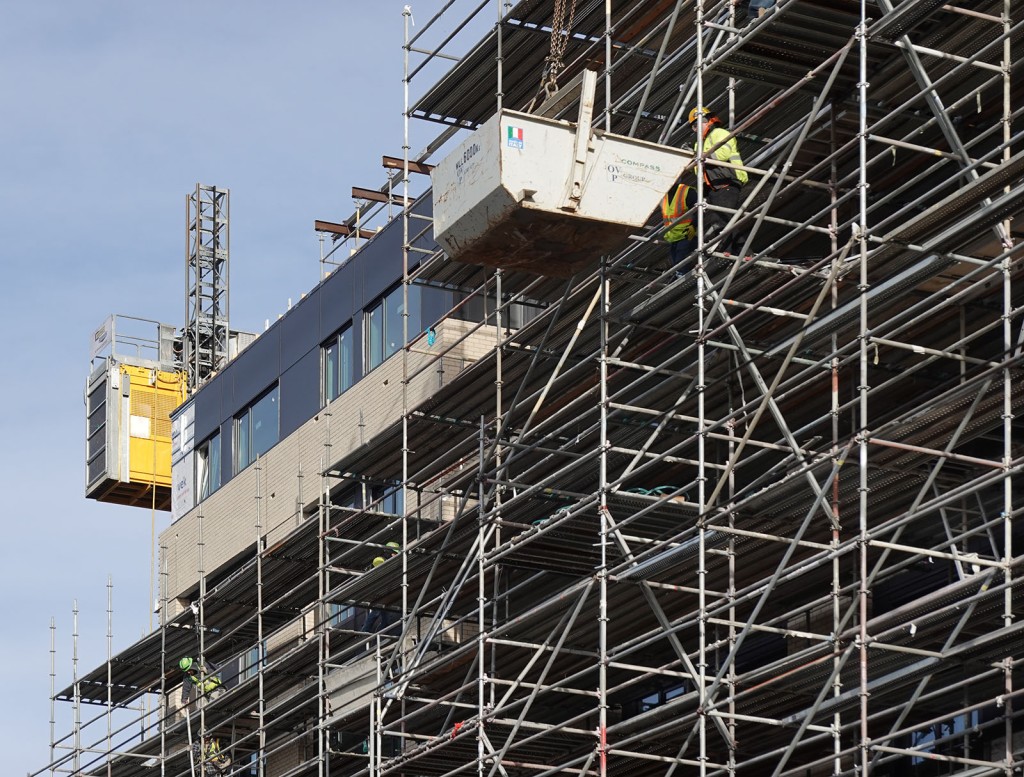
Inside the project, in the central courtyard, the work is farther along, which obviously is harder to see from the street.

And in places the finished colors offer some dramatic contrast.

The floor of the courtyard continues to operate as a materials distribution center. It’s especially useful for the tower crane to have a large, open, flat space for staging and moving materials.
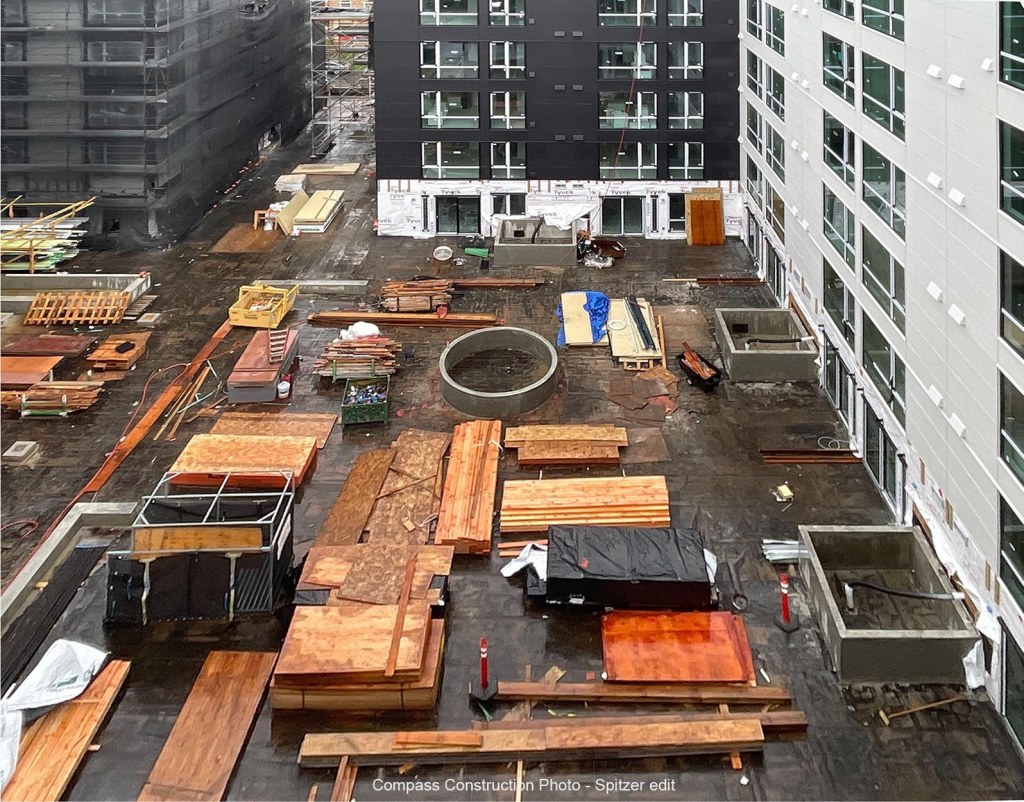
A few things, however, are not movable materials, namely the cast in place concrete planters that will be filled with soil and shrubs as the courtyard gets finished.

The other big surfaces starting to receive finishes and equipment are the roofs. There are many terraces for resident use, some will be private patios associated with specific residential units and others are common roof decks for all residents to use.

These are receiving pedestal pavers set on neoprene pads, designed to let rainwater flow through the joints and fall to the roof underneath which leads the water to drains.
On upper roofs, preparations are being made to support mechanical equipment. Note the yellow, coil springs, design to reduce vibration transfer from the equipment to the roof.

All of this exterior activity is also being accompanied by significant changes on the interior. After drywall has been installed, mechanical/electrical fittings like the Air Conditioning vents are added in the ceiling.
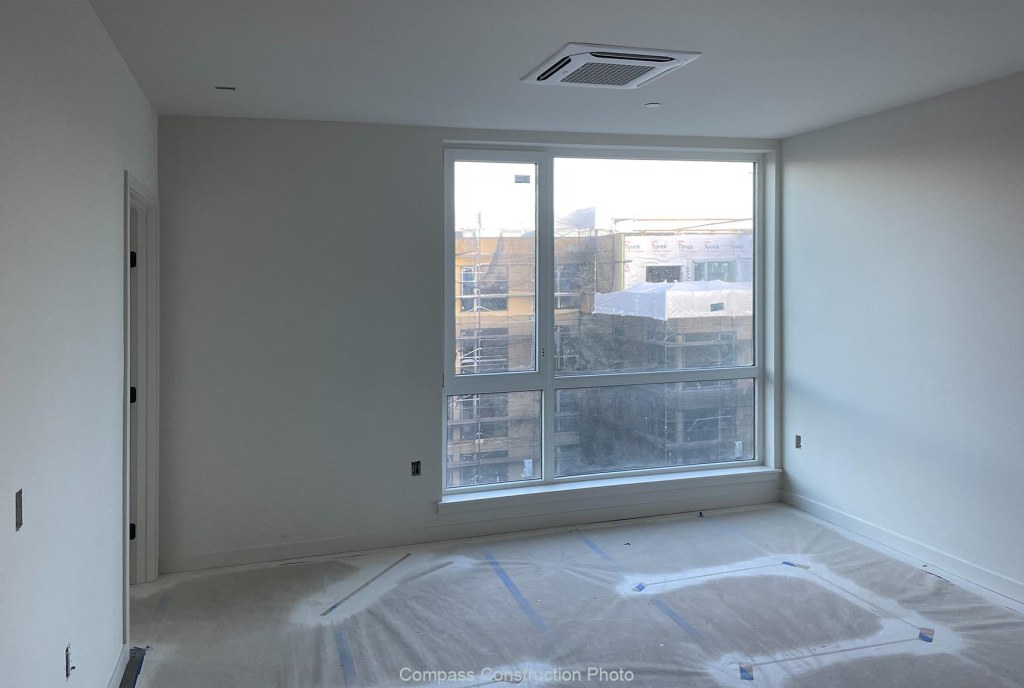
But now we’re also seeing the finished flooring.

A variety of kitchen arrangements, cabinets and fixtures have appeared.
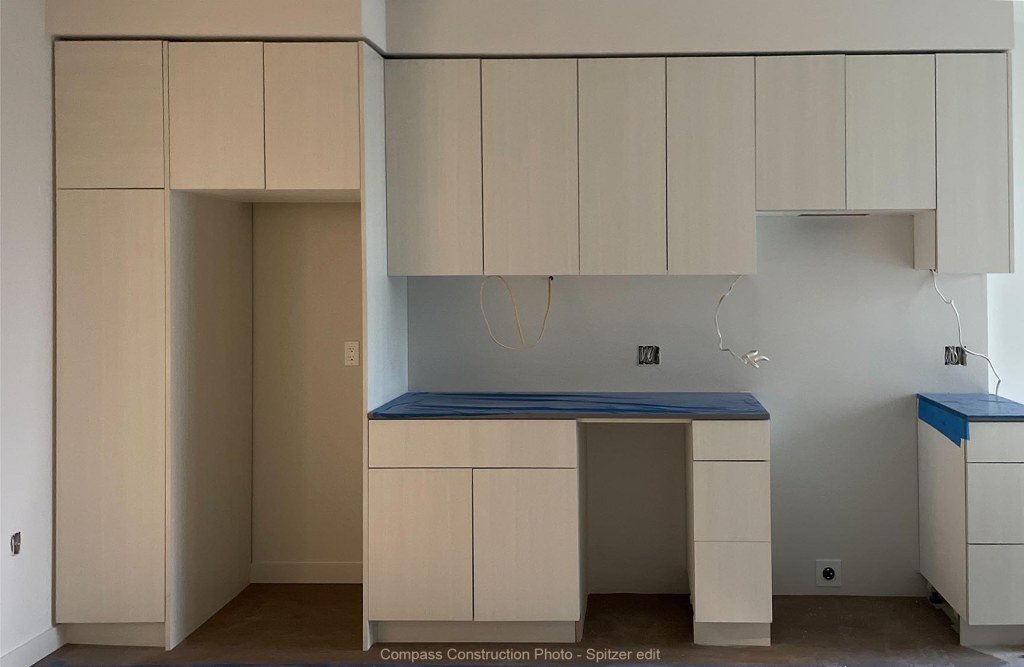
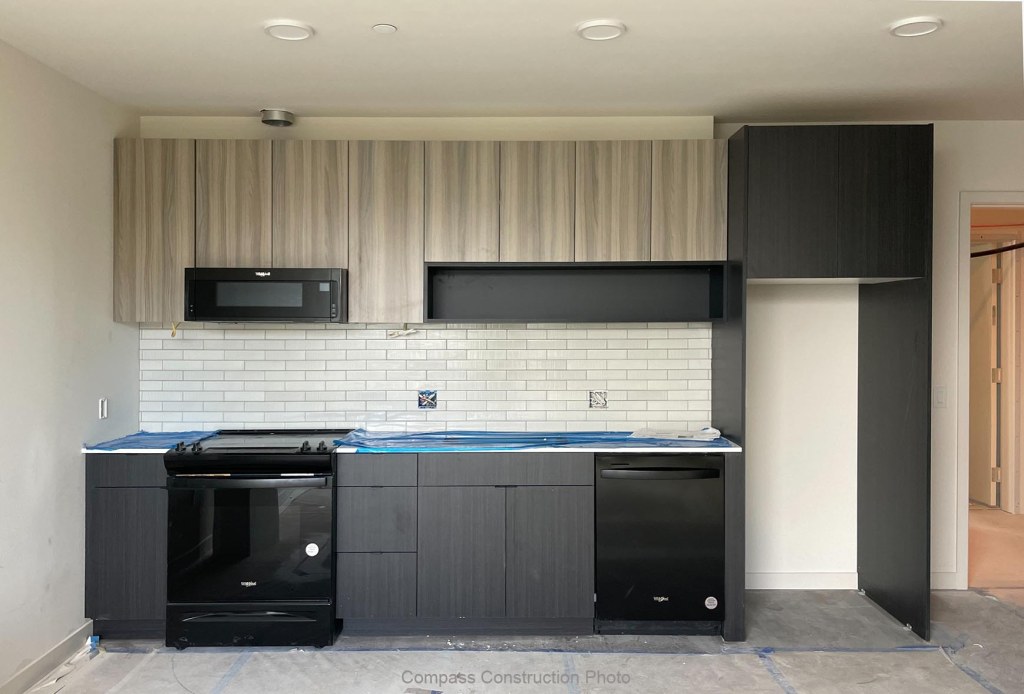

In the near future, more detailed presentations of the interiors will be made as part of the marketing and leasing program.
As a last note, there’s still lots happening at the Safeway level. Here are a couple of examples.

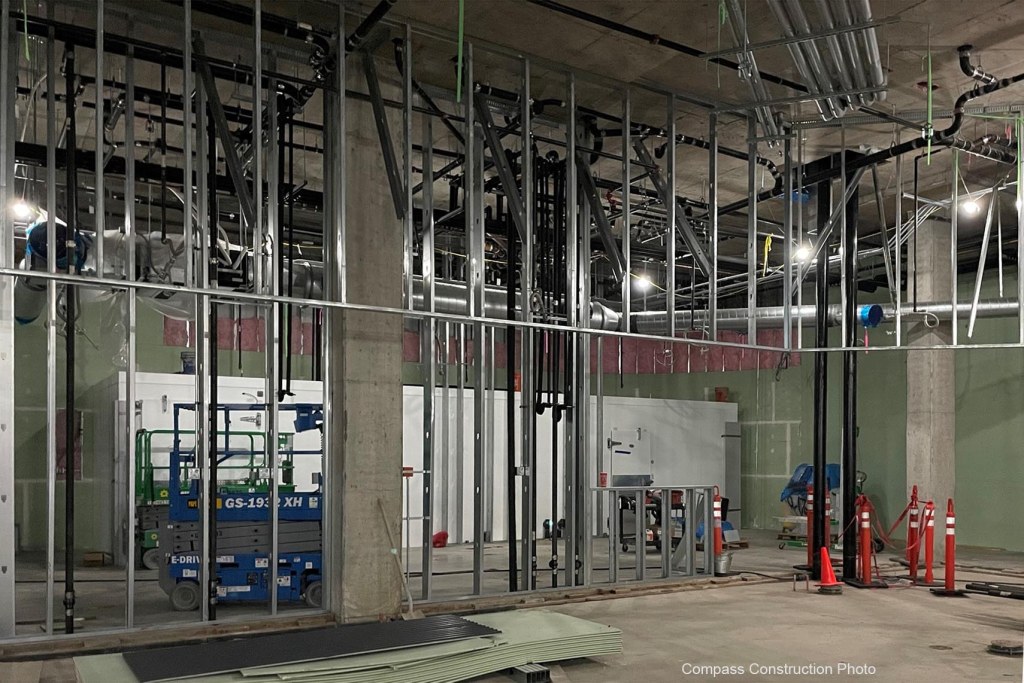
As we head into spring and summer, there will be lots more to see.